Hardware Development Lifecycle
Your Hardware Development Partner. Rapidise offers a structured product development lifecycle tailored to hardware projects, guiding you from initial concept to market launch. Our unwavering support ensures a successful journey at every stage.
Phase 1
SoW, PRD & Architecture

Scope of Work Finalization & A BoM Finalization
Qualcomm
Synaptics
NXP Semiconductor
Nordic Semiconductor
Quectel
Macronix
Micron
Product Requirement Document & Architecture Document
Winbond Electronics
KIOXIA America Inc.
Analog Devices/Maxim Integrated
ST Microelectronics
OSRAM
Panasonic
Texas Instruments
TDK Corporation
Microchip Technology
Renesas
TE Connectivity
AMP Connectors
Molex
Hirose Electric Co Ltd
Samtec
Phase 2
Schematic Design

Power Budget Analysis & GPIO Pin Mapping
High Speed Digital Board Designs
Low Speed Digital Board Designs
RF and Wireless Design Solutions
MCU Designs
Schematic Library Creation & Schematic Drafting
Power-optimized & Battery Operated Designs
Development Platforms
System-on-Modules (SoM)
Embedded Processor Based Designs
BoM Creation & Finalization
Analog and Audio Circuit Designs
Design Estimations/ BOM Optimization
ADCs and DACs
Allegro, OrCAD, Altium, Ki-CAD
Phase 3
Layout Design

Footprint Creation & Get the PCB Stack Up
Library Management
Small Footprints
PCB Stack Up Design
Board Size and Net Count
Signal Integrity
Layout Design & Gerber Release
Power Integrity
Thermal Analysis
Power Distribution
EMI and EMC
Design Rules and Constraints
PCB Fabrication & SMT Assembly
Component Clearance and Mechanical Constraints
Design for Manufacturing (DFM) Analysis
Design for Assembly (DFA) Analysis
Design for Testing (DFT) Analysis
Allegro, OrCAD, Altium, Ki-CAD
Phase 4
Bring up & Product Delivery

Test Cases Preparation, Finalization & PCBA Bring Up EDVT Report
MIPI CSI & DSI, LVDS
Ethernet SGMII & RGMII
Ethernet PHY USB
PCI Express, HDMI, CAN, SATA
GPS, GSM, WiFi, Bluetooth, LTE, NFC
Touch Screen
QA/QC Testing & Final Delivery of Product
AMIC, DMIC, SoundWire, SLIMbus Digital Audio
LDDDR3ILPDDR4ILPDDR4X /LPDDR5
DDR2IDDR3IDDR4 SDRAM
SDIO, SDC, eMMC/UFS, eMCP
Sensors I2C, SPI, UART
RFQ to FDR Rapidise Project Delivery Cycle
Requirements finalization
Product Requirement Specification Phase
Finalizing requirements in an embedded project is an important step in ensuring the successful development and deployment of the system. Here are some key steps and considerations for finalizing requirements in an embedded project
Requirement Identification
Requirement Analysis
Prioritization and Classification
Requirement Traceability
Requirement Validation
Requirement Documentation
Change Management
Architecture Phase
Product Specification
Hardware Architecture
Hardware Design Limitation
Overall BOM Cost
Major Component Selection
Technical Stack
Assumption
Gray Areas
Acceptance Criteria
Risk Factors And Mitigation Plan
Block diagram
Pin Mapping
Power Budgeting
FMEA (Failure Modes and Effects Analysis)
Major Component Selection
When selecting major components for an embedded project, there are several criteria to consider.The specific criteria may vary depending on the nature of the project,but here are some common factors to evaluate:
Submitted by Client
Functional Requirements
Performance
Quality and Reliability
Availability and Longevity
Cost
Compatibility and Interoperability
Development and Support
Scalability and Flexibility
Power Efficiency
Safety and Compliance
By carefully evaluating these criteria and conducting thorough research, you can select major components that align with the project’s requirements, budget, and long-term objectives.
Schematic Design
When creating a schematic design for an embedded project, there are several criteria to consider. The schematic design is a crucial step in defining the electrical and functional aspects of the system. Here are some key criteria to keep in mind:
When selecting major components for an embedded project, there are several criteria to consider. The specific criteria may vary depending on the nature of the project, but here are some common factors to evaluate:
System Requirements
Component Selection
Signal Integrity
Power Distribution
EMI/EMC Considerations
Documentation and Clarity
Revision Control
Collaboration and Feedback
By considering these criteria, you can create a well-designed schematic that effectively represents the electrical aspects of your embedded project and serves as a solid foundation for further development and implementation.
BOM Creation
Component Information
Quantity and Units
Supplier and Pricing Information
Manufacturer and Distributor Support
Alternatives and Second Sources
Lifecycle and Obsolescence Management
BOM Version Control
BOM Creation
Component Datasheets
IPC Standards
Component Geometry
Pad Design
Solder Mask and Paste Mask
Thermal Considerations
Manufacturing Constraints
Silkscreen and Reference Designators
Verification and Validation
Documentation
Keep-out Zones
Component Placement
Signal Integrity
Thermal Management
Power Distribution
Iterative Optimization
Manufacturing and Assembly
Design for Testing (DFT)
Documentation and Clarity
Design Rules and Constraints
Electromagnetic Compatibility
Component Clearance and Mechanical Constraints
Electro mechanical verification
Dimensional Compatibility
Mechanical Stress and Strain
Electrical Connection
Electrical Grounding
EMI/EMC Compliance
Mechanical and Electrical Safety
Functional Integration
Thermal Management
Environmental Durability
Documentation and Standards Compliance
PCB Layout
Component Placement
Signal Integrity
Power and Ground Planes Incorporate
Routing and Trace Considerations
Thermal Management
Design for Manufacturing (DFM)
Design for Testing (DFT)
EMI/EMC Considerations
Component and Footprint Selection
Documentation and Verification
Revision Control
Board Bring up
Power Supply
Component Placement
Solder Joints
Signal Integrity
Clock and Timing
Power Integrity
Functional Testing
Thermal Management
Compliance and Standards
Hardware Firmware Integration (dump code)
The criteria for hardware-firmware integration, specifically when it comes to integrating firmware (also known as “dump code”) with hardware, typically involve the following considerations
Firmware Compatibility
Hardware Initialization
Communication Interfaces
Register Configuration
Peripheral Integration
Memory Management
Error Handling and Fault Tolerance
Real-Time Constraints
Integration Testing
QA/QC Testing
Test Planning
Functional Testing
Performance Testing
Usability Testing
Compatibility Testing
Security Testing
Regression Testing
Stress and Load Testing
Compliance Testing
Documentation Review
Bug Tracking and Reporting
Continuous Improvement
Final Testing
System Integration Testing
End-to-End Testing
User Acceptance Testing (UAT)
Performance and Scalability Testing
Security and Penetration Testing
Compatibility Testing
Accessibility Testing
Regression Testing
Reliability and Stability Testing
Disaster Recovery and Backup Testing
Compliance and Certification Testing
Documentation and Release Readiness
User Feedback Incorporation
Shipment & Release
Quality Assurance
Regulatory Compliance
Manufacturing Readiness
Inventory Management
Documentation and Manuals
Order Fulfillment
Logistics and Shipping
Export and Import Compliance
Component and Footprint Selection
Documentation and Verification
Revision Control
PCB Layout
Component Placement
Signal Integrity
Power and Ground Planes Incorporate
Routing and Trace Considerations
Thermal Management
Design for Manufacturing (DFM)
Design for Testing (DFT)
EMI/EMC Considerations
Component and Footprint Selection
Documentation and Verification
Revision Control
Industries We Serve
Rapidise caters for many industries and offers specialized and unique industrial solutions within sectors. We appreciate that each industry has its strengths and weaknesses, and we tap into it to facilitate your business objectives.
Our Technology Marketplace
Accelerate your Product Development with a Ready made HW, SW, or AI Solution
Browse the Rapidise tMarket for a vast selection of matured accelerator solutions ready to implement into your product now which decrease down-stream costs and accelerate your time-to market. SOMs & SOCs, SDKs, AI Models & Libraries, and more…
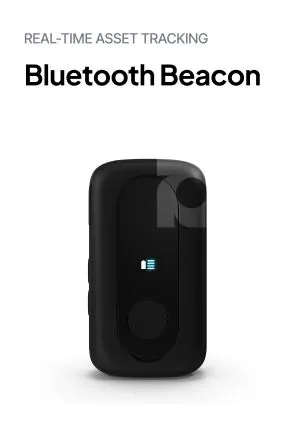
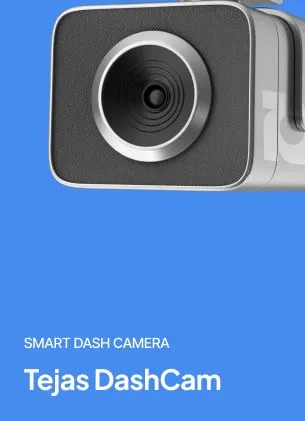
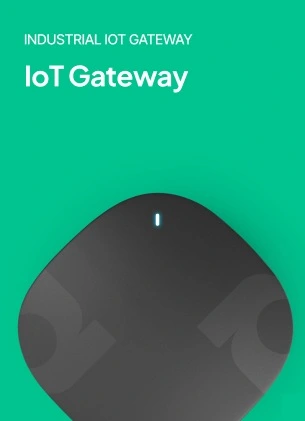
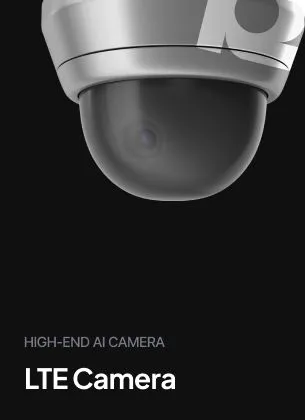
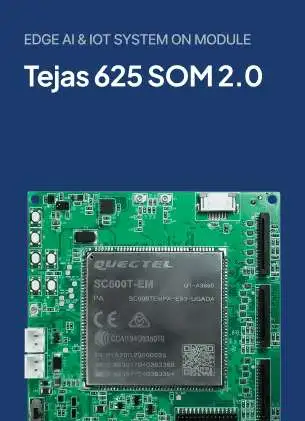